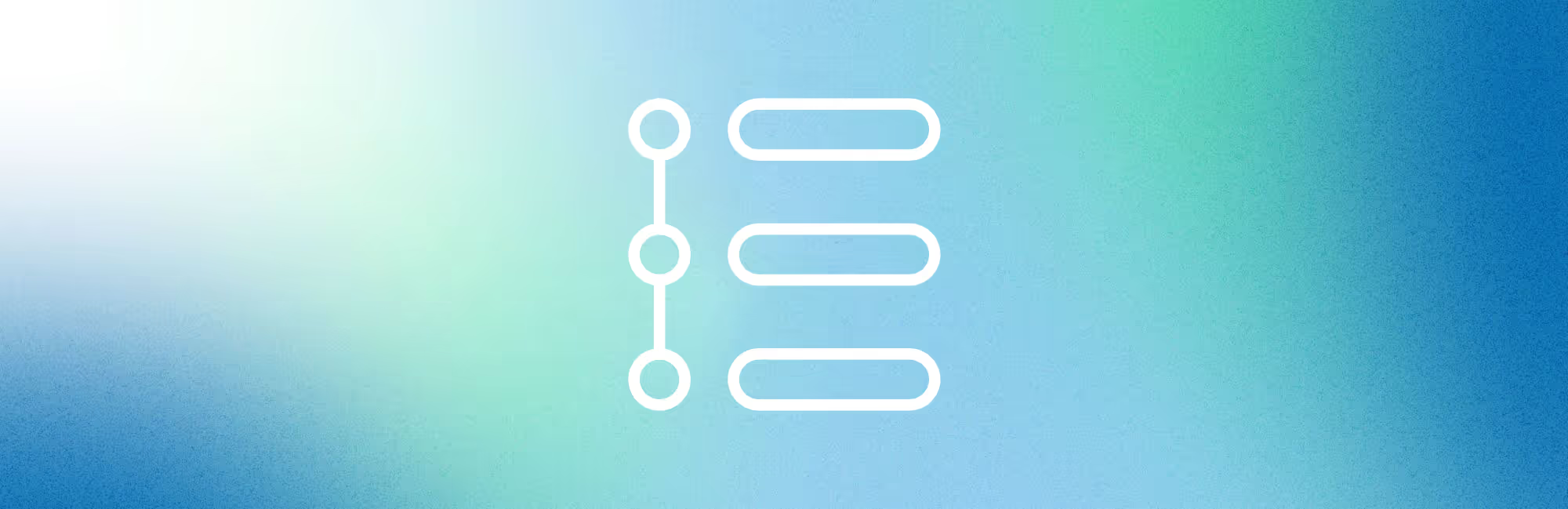
For organizations that rely on heavy machinery and equipment, reducing downtime and maximizing equipment reliability is crucial to maintaining operational efficiency and profitability. Mean time between failures (MTBF) is a key metric that can help achieve this goal. By implementing an effective MTBF program, organizations can identify, address, and prevent equipment failures, ultimately reducing downtime and increasing overall productivity. In this blog post, we will discuss the key steps to implement an MTBF program for your organization.
Define your goals and objectives
The first step in implementing an MTBF maintenance program is to define your specific goals and objectives. What do you hope to achieve by reducing downtime and increasing equipment reliability? Are you aiming for a specific MTBF target, or do you want to minimize costly unplanned downtime using MTBF software? Having clear objectives will guide your program and help you measure its success.
Identify critical equipment
Not all equipment within your organization is equally important. Some machinery may have a more significant impact on your operations than others. Identify and prioritize critical equipment that, if it were to fail, would have a substantial impact on production, safety, or other critical factors. Focusing on critical equipment allows you to allocate resources more efficiently.
Gather data and historical records
To establish a baseline for your MTBF program, you need to gather historical data on equipment failures. Analyze past MTBF maintenance records, failure reports, and downtime incidents to identify patterns and common causes of failures. This data will be crucial for creating MTBF analysis reports to understand the current state of your equipment and where improvements can be made.
Implement preventive maintenance
If you are wondering how to improve MBTF, you can rely on preventive maintenance. Preventive maintenance is the cornerstone of any successful MTBF program. Develop a robust preventive maintenance schedule for your critical equipment. This schedule should include regular inspections, routine maintenance tasks, and the replacement of wear-and-tear parts. By proactively addressing potential issues, you can extend the life of your equipment and reduce the risk of unexpected failures.
Condition monitoring and predictive maintenance
To further improve equipment reliability, consider implementing condition monitoring and predictive maintenance techniques. These strategies involve using sensors and monitoring systems to track equipment performance in real-time. By analyzing data and trends, you can predict when maintenance is required, allowing you to address issues before they lead to a breakdown.
Conduct root cause analysis
When equipment failures do occur, it's essential to conduct a thorough root cause analysis. Identify why the failure happened, whether it's due to human error, design flaws, or other factors. By addressing the root causes, you can prevent similar failures in the future and continually improve your MTBF program.
Invest in training and education
Equip your maintenance and operational teams with the necessary skills and knowledge to maintain and operate equipment effectively. Regular training and education sessions can help prevent common mistakes and ensure that your workforce is equipped to handle the equipment properly, extending its lifespan.
Focus on continuous improvement
An effective MTBF program is not a one-time effort but an ongoing process of continuous improvement. Regularly review your program's effectiveness, gather feedback from your teams, and make necessary adjustments to meet your objectives. Technology and industry best practices are constantly evolving, so stay up-to-date to keep your program effective.
Partner with a trusted service provider
Partnering with a service provider that specializes in MTBF maintenance program implementation is essential for organizations looking to stay competitive. And TMA Systems can be your trusted partner in this journey. With our cutting-edge solution — WebTMA — and extensive experience in the field of maintenance management, we offer a comprehensive suite of tools designed to streamline your maintenance processes and optimize asset performance. Our user-friendly software equips you with the ability to monitor equipment performance, schedule preventive maintenance, and accurately predict when assets may fail. By focusing on proactive maintenance, we help you increase the MTBF of your critical assets, minimizing costly downtime and improving overall reliability. Visit our website to learn more or request a demo now.
Ready for a Demo?
Interested in taking this to the next level? Sign up for a free demo with a TMA Systems Account Executive. Enter your email below and we will reserve a time for you to test drive WebTMA.
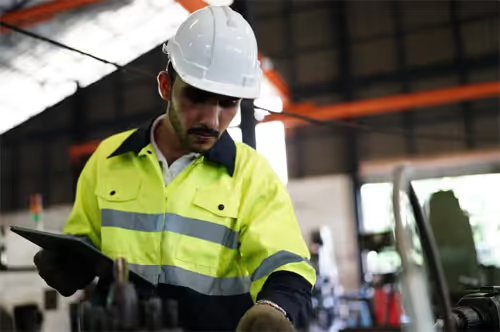
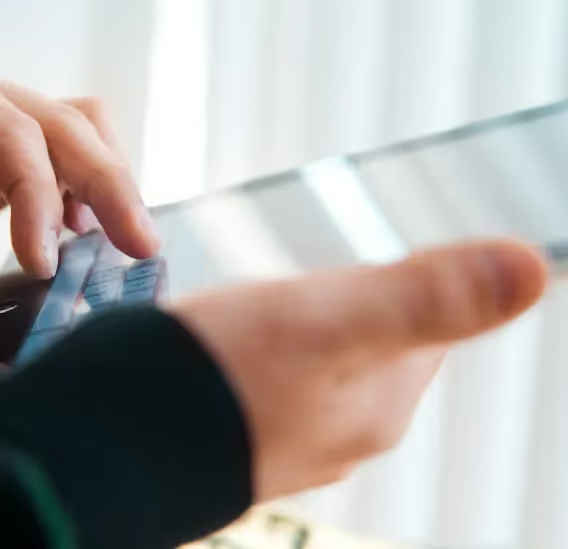
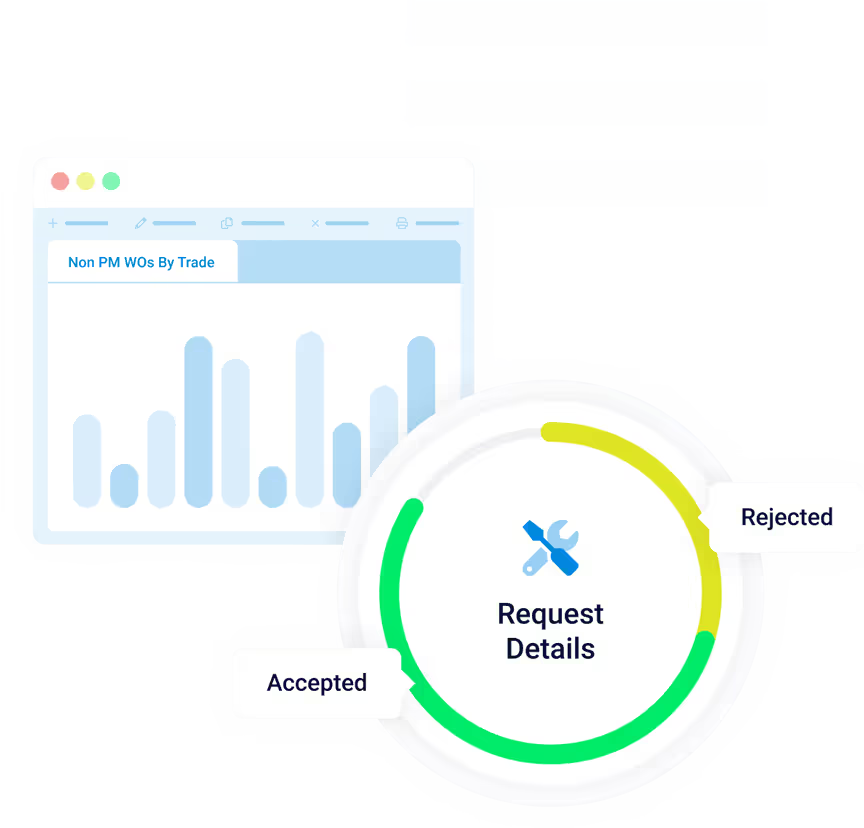