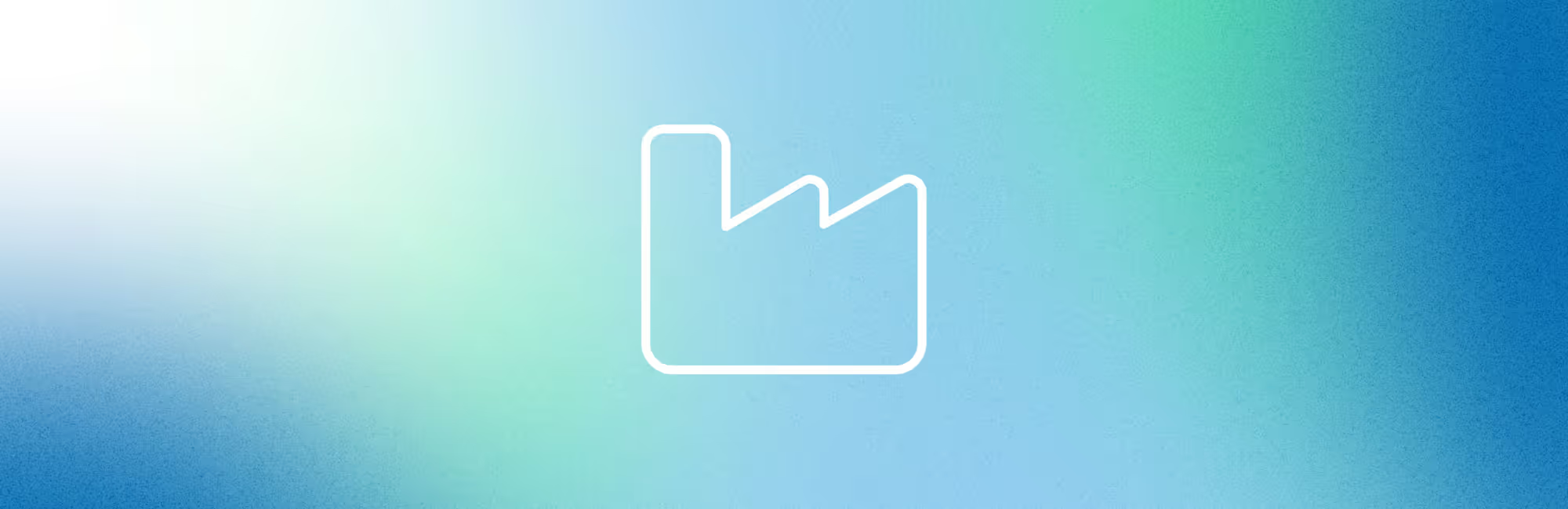
Industry 4.0, also known as the Fourth Industrial Revolution, is characterized by the fusion of advanced technologies and digitization in various industries. It has transformed traditional manufacturing processes and has paved the way for a new era of industrial production. The impact of Industry 4.0 on maintenance and software like Computerized Maintenance Management Systems (CMMS) and Calibration Management is substantial, as it has the potential to optimize asset management and reduce downtime. In this article, we will explore the impact of Industry 4.0 on maintenance and software, and how it affects different industries.
What is Industry 4.0?
Industry 4.0 refers to the integration of advanced technologies such as the Internet of Things (IoT), artificial intelligence (AI), machine learning, and big data analytics. The main objective of Industry 4.0 is to improve the efficiency and productivity of manufacturing processes by creating a smart factory that is capable of self-optimization, self-configuration, and self-diagnosis. It encompasses a range of digital technologies that can be applied to various industries, including manufacturing, healthcare, energy, transportation, and more.
Impact of Industry 4.0 on Maintenance
The implementation of Industry 4.0 technologies has a significant impact on maintenance. It has transformed traditional maintenance practices and has made them more efficient and cost-effective. With the integration of IoT and AI, maintenance can be performed with a predictive approach, rather than reactive or preventive. Predictive maintenance uses data analysis to identify potential equipment failures before they occur, thereby reducing downtime and maintenance costs.
In addition to predictive maintenance, Industry 4.0 has also introduced the concept of augmented reality (AR) in maintenance. AR allows maintenance technicians to access real-time information about equipment and processes, which can help identify issues and perform maintenance tasks more effectively. For example, AR can be used to provide step-by-step instructions for complex maintenance tasks, which can help reduce the risk of errors and improve efficiency.
Impact of Industry 4.0 on CMMS and Calibration Management
CMMS and Calibration Management software are critical tools for maintenance management in many industries. The implementation of Industry 4.0 technologies has a significant impact on these software systems, as it enables them to integrate with other technologies like IoT and AI. This integration allows for real-time data collection and analysis, which can help maintenance managers make informed decisions about equipment maintenance and calibration.
For example, CMMS software can be used to monitor equipment performance and trigger maintenance alerts based on data analysis. Similarly, Calibration Management software can use IoT sensors to collect real-time data about equipment performance, which helps maintenance managers schedule calibration tasks. The integration of these software systems with Industry 4.0 technologies can help reduce downtime, improve efficiency, and reduce maintenance costs.
Impact of Industry 4.0 on Different Industries
The impact of Industry 4.0 on maintenance and software varies across industries. In the manufacturing industry, Industry 4.0 has transformed traditional manufacturing processes making them more efficient and cost-effective. Predictive maintenance and AR can help reduce downtime and improve productivity, while the integration of CMMS and Calibration Management software with IoT and AI can help optimize asset management.
In the healthcare industry, Industry 4.0 has introduced the concept of smart hospitals, which use IoT and AI to optimize patient care and streamline processes. Maintenance and software play a critical role in ensuring the smooth operation of these facilities. Predictive maintenance and AR can help reduce equipment downtime and improve the quality of patient care, while CMMS and Calibration Management software can help optimize equipment maintenance and calibration.
In the energy industry, Industry 4.0 has the potential to optimize energy consumption and reduce carbon emissions. Maintenance and software play a critical role in ensuring the smooth operation of energy production facilities. Predictive maintenance and AR can help identify potential equipment failures before they occur. CMMS and Calibration Management software can be used to schedule maintenance and calibration tasks, ensuring that equipment is operating at optimal levels and reducing energy waste.
In the transportation industry, Industry 4.0 has the potential to improve safety and reduce transportation costs. Maintenance and software play a critical role in ensuring the safe and efficient operation of vehicles and transportation systems. Predictive maintenance and AR can help identify potential safety issues before they occur, while CMMS and Calibration Management software can help schedule maintenance and calibration tasks, ensuring that vehicles are operating at optimal levels.
At TMA Systems, we understand the importance of Industry 4.0 and the impact it has on maintenance and software in various industries. That's why we offer a range of innovative software solutions that integrate with Industry 4.0 technologies including IoT and big data analytics. Our CMMS and Calibration Management software can assist in optimizing asset management, reducing downtime, and improving efficiency across different industries.
If you're interested in learning more about our software solutions and how they can help your business thrive in the era of Industry 4.0, contact us today. Our team of experts is ready to answer your questions and help you find the right software solutions for your needs. Let's work together to embrace the future of maintenance and software with Industry 4.0.
Ready for a Demo?
Interested in taking this to the next level? Sign up for a free demo with a TMA Systems Account Executive. Enter your email below and we will reserve a time for you to test drive WebTMA.
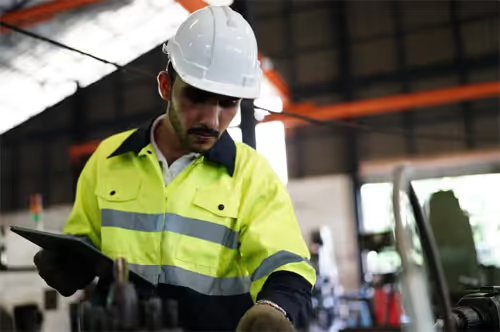
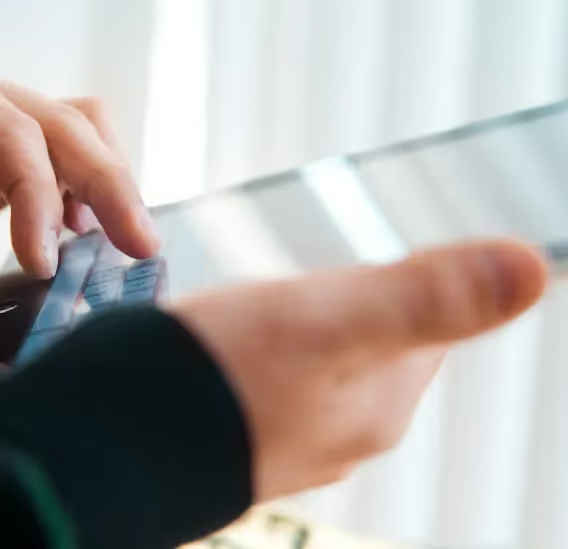
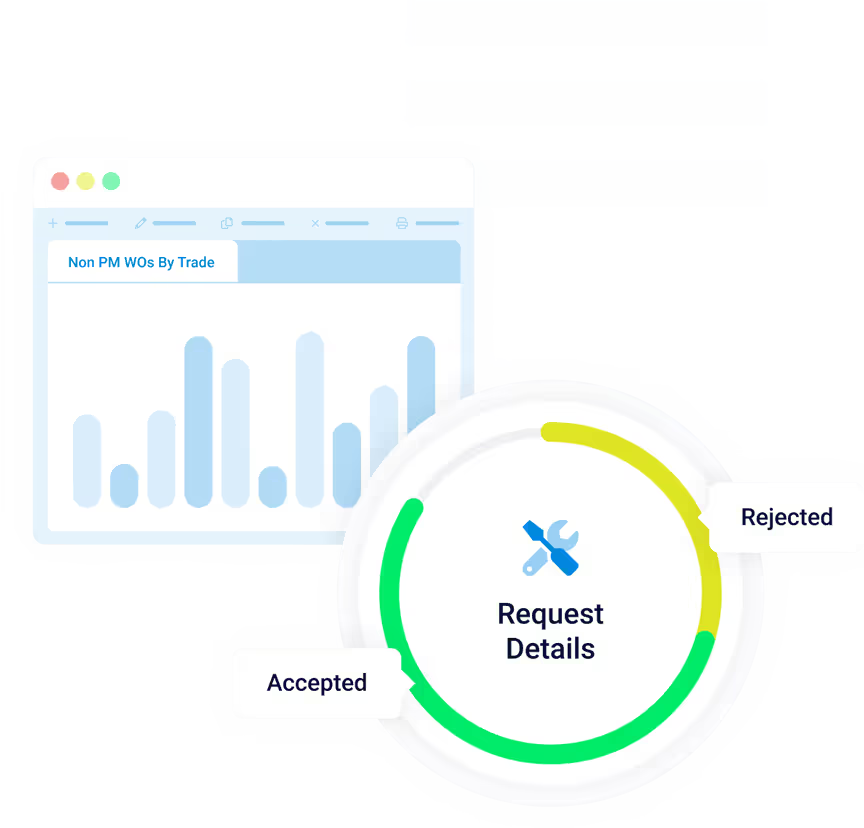