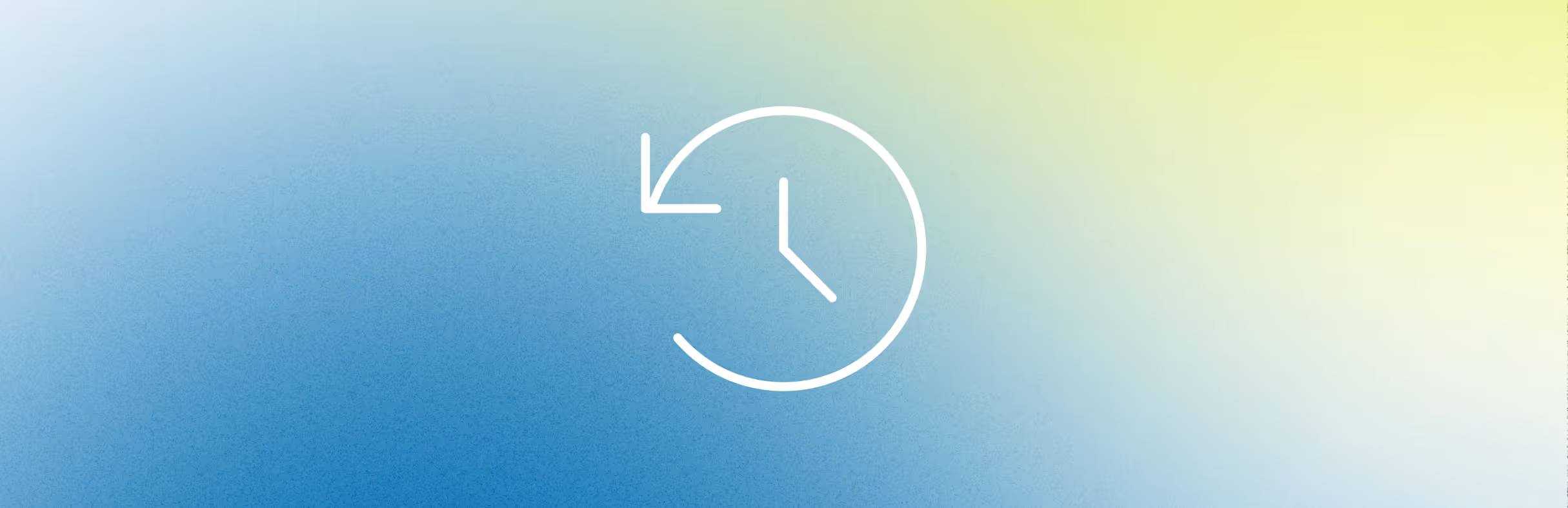
Imagine a world where equipment seldom broke down and halted operations unexpectedly. A world where business processes could potentially be completed ahead of schedule. This isn’t a dream scenario, this can be a reality—through preventive maintenance. Implementing a proactive maintenance approach reduces the likelihood of equipment failure and minimizes unplanned downtime. It maximizes productivity, increases efficiency, and reduces costs in the long run. As the benefits of preventive maintenance are getting more widely recognized, companies are increasingly leveraging this approach to achieve operational excellence and maintain a competitive advantage.
Why is preventive maintenance essential?
The preventive maintenance market is expected to reach $15.9 billion by 2026. It saves money by reducing the need for costly repairs and equipment replacements. Detection of potential asset issues facilitates predictive maintenance, averting emergency repairs and unscheduled downtime. Overall equipment effectiveness (OEE) and equipment performance optimization are additional advantages of implementing a preventive maintenance strategy. Equipment in its optimum condition functions at peak efficiency and consumes relatively less energy.
IoT and other advanced technologies have made preventive maintenance more predictive and effective. The use of advanced technology helps to identify potential safety hazards and lowers the risk of accidents and injuries to create a safer work environment. Preventive maintenance practices ensure that equipment complies with regulatory standards, avoiding potential fine as and legal liabilities.
Real-world impact of preventive maintenance
A leading e-commerce and technology company recently invested heavily in preventive maintenance technologies to support its massive logistics operations worldwide. Designed for its fulfillment centers, the preventive maintenance program used data analytics and machine learning to identify potential operational issues before they became major problems. The global organization saved nearly $22.75 million, reduced downtime by 69%, increased productivity, and improved overall operational efficiency.
One of the leading package delivery companies in the world implemented a preventive maintenance program in 2020 for its aircraft fleet. By doing so, it reduced maintenance costs and improved the overall fleet reliability as it ensured that its aircrafts remained in excellent condition and rarely required unscheduled maintenance.
Similarly, in 2021, a global leader in energy management and automation solutions implemented a preventive maintenance program to guarantee that its manufacturing processes were as efficient and effective as possible. In the same year, one of the world's largest oil and gas companies employed a preventive maintenance program for its oil refineries to increase productivity while reducing costs.
Known for its "Total Productive Maintenance" (TPM) program, one of the largest automobile manufacturers in the world emphasizes preventive maintenance to improve equipment reliability, reduce downtime, and increase productivity. The program has been credited with helping the automotive leader become one of the most renowned and reliable automakers in the world.
These are just a few examples of how enterprises across industries are adopting preventive maintenance to achieve operational excellence and improve the employee experience.
Build your preventive maintenance program with TMA Systems
Implementing an effective preventive maintenance system is essential to keep your equipment operating at its best. TMA Systems, a trusted provider of facilities and asset management solutions, can help you in this journey. With our CMMS/EAM solution, WebTMA, you can easily manage and track your facilities, equipment, and assets. Our software will help you to identify high-risk equipment, track usage and performance, and analyze maintenance costs and downtime.
Incorporate a preventive maintenance strategy today and transform your business operations. Don't let unexpected equipment breakdowns and downtime slow productivity and reduce revenue. By implementing a proactive maintenance strategy, you can maximize your equipment's lifespan, increase efficiency, and reduce costs in the long run. Join the growing number of companies achieving operational excellence and maintaining a competitive advantage with TMA Systems.
Schedule a demo today and invest in the future of your assets.
Ready for a Demo?
Interested in taking this to the next level? Sign up for a free demo with a TMA Systems Account Executive. Enter your email below and we will reserve a time for you to test drive WebTMA.
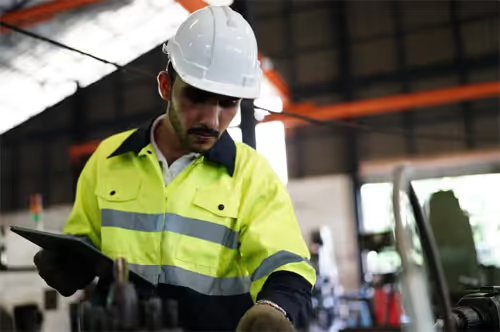
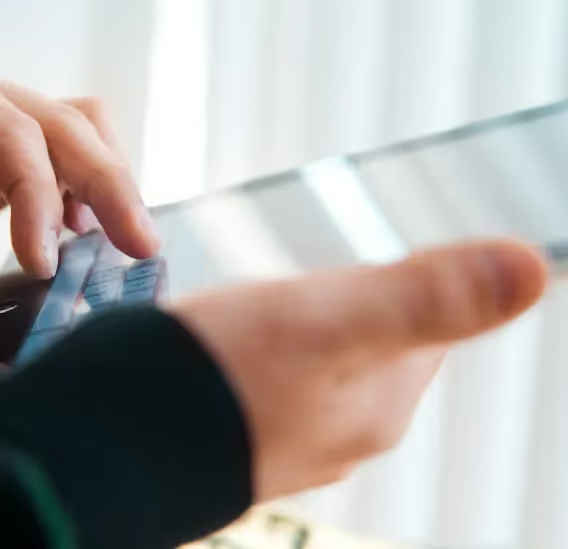
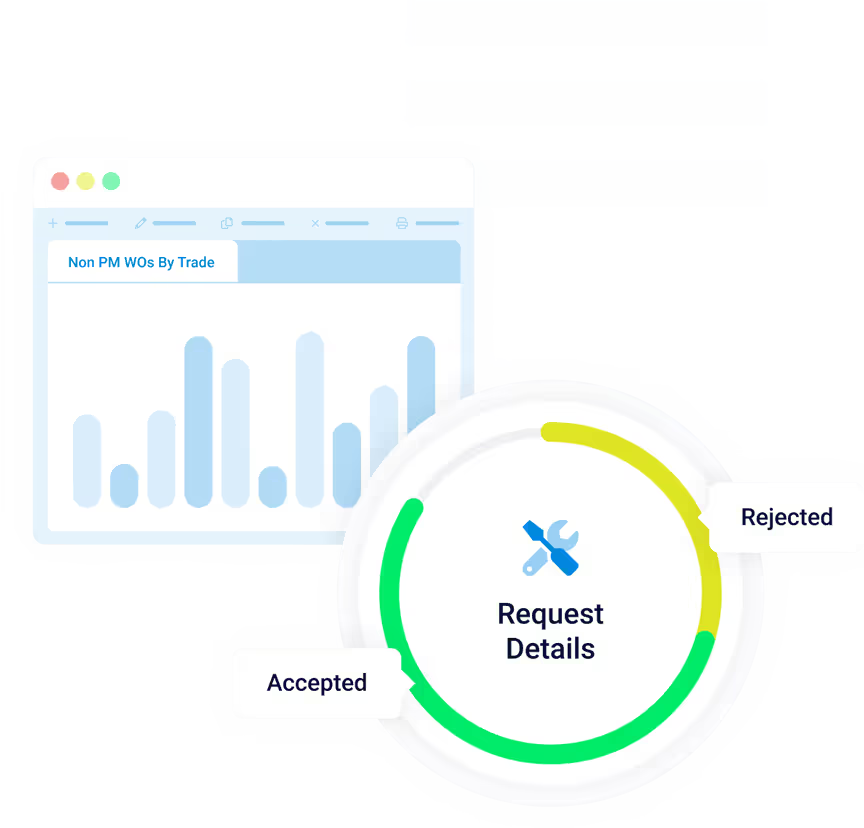